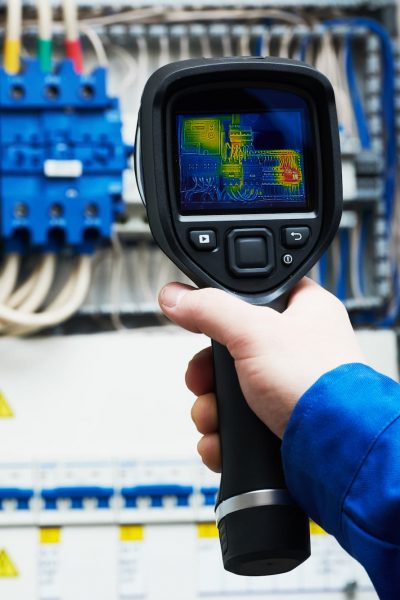
Pioneer Power Group offers infrared scans to keep your staff safe and your equipment intact at your commercial or industrial facility. This process is straightforward and non-invasive.
Importance of Infrared Scanning
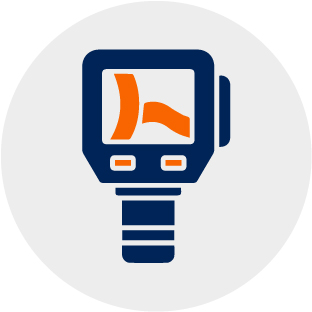
Infrared scanning, also referred to as thermal imaging or thermographic inspection, is essential for ensuring the safety and reliability of electrical systems. This non-destructive testing technique detects heat patterns or “hot spots” that could signal overloads, loose connections, or equipment failures. By using infrared scanning technology, you can prevent expensive downtime, improve safety, and maintain the efficient operation of electrical equipment.
Why is Electrical Infrared Scanning Needed?
Preventing Equipment Failures and Downtime:
Routine infrared scanning helps prevent equipment failures by identifying early signs of electrical problems, such as excessive heat in circuit breakers, switchgear, transformers, or electrical panels. Detecting these issues early allows for timely repairs, minimizing the risk of unexpected outages and reducing downtime.
Improving Energy Efficiency and Reducing Costs:
Regular infrared scans help optimize energy efficiency by identifying areas where electrical systems are wasting energy due to faulty or inefficient components. Addressing these issues leads to significant cost savings on energy bills and reduces the need for costly emergency repairs.
Detecting Overheated Electrical Components:
Electrical systems are vulnerable to overheating due to factors such as loose connections, circuit overloads, faulty equipment, or unbalanced loads. An infrared scan detects these anomalies by capturing thermal images of electrical components, highlighting areas with abnormal heat levels that could signal an impending failure or fire hazard.
Ensuring Electrical Safety and Compliance:
Overheated electrical components are a major cause of electrical fires and safety incidents. By conducting regular infrared scans, organizations can ensure compliance with industry safety standards and regulations, reducing fire risk and protecting personnel and assets.
What can an Infrared Scan detect?
- System Overloads/Unbalanced loads
- Loose and deteriorated connections
- Cooling system defects
- Low liquid levels and oil circulation issues
- Open circuits
Key Benefits of Electrical Infrared Scanning
- Cost Savings: Prevents costly repairs and downtime by identifying issues early, which can avoid major breakdowns and extend the lifespan of equipment. Early detection helps in budgeting for maintenance before problems escalate.
- Enhanced Safety: Detects potential hazards such as overheating or electrical faults, reducing the risk of accidents and injuries. By addressing issues before they become severe, it ensures a safer working environment for staff.
- Operational Efficiency: Ensures optimal performance and longevity of electrical systems by addressing inefficiencies or malfunctions promptly. This proactive approach minimizes disruptions and keeps operations running smoothly.
- Non-Destructive: Offers a non-invasive method for inspecting equipment without disrupting normal operations. This allows for continuous monitoring without the need for shutdowns or extensive downtime.
Electrical infrared scanning is an essential practice for maintaining the safety, efficiency, and reliability of electrical systems. It provides a proactive approach to identifying and resolving potential problems before they cause damage, downtime, or safety incidents. By investing in routine infrared inspections, organizations can achieve long-term cost savings, improve energy efficiency, and ensure compliance with industry standards.